For any new features, suggestions and bugs create an issue on. The new object to get params in React Navigation 5 is: Source https://stackoverflow.com/questions/61859411, Community Discussions, Code Snippets contain sources that include Stack Exchange Network, Save this library and start creating your kit. The shoulder servo takes the most strain from the weight and inertia of the rest of the arm. Get full pictogram instructions and give yourself an extra hand at DesignSpark: https://www.rs-online.com/designspark/build-and-program-a-braccio-robot, Panasonic PhotoMOS Photovoltaic MOSFET High-Power Drivers, A selection of Robotics articles for further reading, United States of America Huntington Convention Center of Cleveland, Ohio, Malasia Malaysia International Trade and Exhibition Centre, United Kingdom Coventry Building Society Arena, Coventry. Braccio.ServoMovement(20, 0, 15, 180, 170, servo5, 73); else if (realservo >=6000 && realservo < 6180){. Peter Corke, https://www.hackster.io/rpatterson/gobilda-robot-arm-mechanical-design-3051ac, https://www.arduino.cc/en/Guide/Braccio#braccio-shield, https://content.arduino.cc/assets/Braccio-Shield-V1.pdf, http://www.farnell.com/datasheets/2575116.pdf?_ga=2.151369337.1936105882.1517985527-654667508.1508905608. Elecrow CrowPi L is an 11.6-inch laptop shell based on Raspberry Pi 4 designed for STEM education with. Don't know if it is helpful, but here is a piece of the code. This library is distributed in the hope that it will be useful, The DH results (see figure below) are I confess still counter intuitive to me, but they modelled and animated fine in Matlab. Making statements based on opinion; back them up with references or personal experience. It has 7 star(s) with 5 fork(s). https://www.jameco.com/jameco/workshop/howitworks/how-servo-motors-work.html. The DH results (see figure below) are I confess still counter intuitive to me, but they modelled and animated fine in Matlab. The mistake I made was the paper scribbling. The next part was to fix the jumper to each of the copper strips. An IMU can either be gimballed or strapdown, outputting the integrating quantities of angular velocity and acceleration in the sensor/body frame. Now as I said earlier Braccio comes with certain libraries and coding for the same is very different. Imagine a cuboidal box with a small ball inside it, like in the picture above. pinMode(12,OUTPUT); digitalWrite(12,HIGH); Having looked more closely, I can see what, Power supply to Tinkerkit's braccio fails when working with firmata.js, https://store.arduino.cc/tinkerkit-braccio, Measurable and meaningful skill levels for developers, San Francisco? it will only rotate as much we want and then stop and wait for next signal to take further action. As one would expect, some things work fine, providing excellent performance, but others still need improvements. arduino-library-braccio-robot has 0 bugs and 1 code smells. The shaft of the servo. The attempt is to control 3 servos with mpu6050. https://www.youtube.com/watch?v=ibiFqtv0j-Y, http://www.instructables.com/id/DIY-Bend-Sensor-Using-only-Velostat-and-Masking-T/. The design places the centre of mass of servos internally along the line of the robot arm rather than to the side (see figure below). Out of these, the cookies that are categorized as necessary are stored on your browser as they are essential for the working of basic functionalities of the website. Braccio.ServoMovement(20, 90, 90, 90, 90, 90, 73); Once the calibration was done I ran a few examples codes to see the working of the machine. Inertial Measurement Units (IMUs) is a self-contained system that measures linear and angular motion usually with a triad of gyroscopes and triad of accelerometers. The robot arm links are manufactured from reasonably robust plastic. I then packed all the layers and this is the final flex sensor. However the downside of the design is that the servo shaft directly bears all the forces put on the joint. https://www.youtube.com/watch?v=8wvEauCCvio. The video for the same can be found below. Connect and share knowledge within a single location that is structured and easy to search.

Has anyone already faced something like this? I don't see how that achieves a soft start as the servos are not being controlled whilst that's happening. but WITHOUT ANY WARRANTY; without even the implied warranty of I placed the insulation tape, on them the plastic sheet and then the copper strip. These cookies do not store any personal information. The design places the centre of mass of servos internally along the line of the robot arm rather than to the side (see figure below). How can I change an element's class with JavaScript? To watch the graphical interface of the movement we have to use Processing. The above link was really really useful in helping me understand how to make it possible. Arduino says the new robotic arm is made of recycled and eco-friendly materials with the plastic parts using Ecoallene, instead of the ABS plastics. Code complexity directly impacts maintainability of the code. Are Banksy's 2018 Paris murals still visible in Paris and if so, where? Gyroscopes work on the principle of Coriolis acceleration. This is caused as a result of the inertia of the moving fork. The library offers easy access to the data from the onboard Arduino Braccio, and provides moves the Arduino Braccio. This library is free software; you can redistribute it and/or, modify it under the terms of the GNU Lesser General Public, License as published by the Free Software Foundation; either. A small library to control the Tinkerkit Braccio robot arm. Cholera Vaccine: Dubai? The library for the same has to be found in the below link: https://github.com/arduino-org/arduino-library-braccio.

Next, open the example program from File --> Examples --> MPU6050 --> Examples --> MPU6050_DMP6. Should I try to connect the servos directly on Arduino without the shield? Powered by Trac 1.4.1 Although I can't find any documentation for the Braccio shield, if you look at the Braccio library source code, you'll see they do something "odd" in void _Braccio::_softStart(). .

See the GNU. The video of testing can be found below at the end of page. This library is free software; you can redistribute it and/or arduino-library-braccio-robot has no issues reported. Question on solving partial derivative in probability theory. https://www.arduino.cc/en/Guide/Braccio. You can familiarise yourself with the ideas behind it to begin programming robots from the ground up for yourself. float voltage = sensorValue * (5.0 / 1023.0); double gyroYrate = -((double)gy / 100.0); double gyroZrate = -((double)gz / 100.0); // Braccio.ServoMovement(0, gyroZangle, gyroYangle/2, gyroYangle, gyroYangle/2, gyroXangle, 10); //Braccio.ServoMovement(15, gyroZangle, gyroYangle/2, gyroYangle, gyroYangle/2, gyroXangle, 73); //Braccio.ServoMovement(15, gyroZangle, gyroYangle/2, gyroYangle, gyroYangle/2, gyroXangle, 10); Robotics is something that completely new to me. 468). The PWM signal is fine.
.png)
You can typically identify the number of degrees of freedom by the number of actuators on the robot arm. There are three pairs of opposite walls in a cuboid. This commit does not belong to any branch on this repository, and may belong to a fork outside of the repository. When the shaft of the motor is at the desired position, the power supplied to the motor is stopped. But opting out of some of these cookies may affect your browsing experience. Uploaded the program to Arduino but keep in mind the port used and the bandwidth needs to be changed to 115200.

I have an Arduino UNO and have uploaded StandardFirmata on it. The degrees of freedom, or DOF, is a very important term to understand. Which is nice in terms of weight distribution. This saves a lot of wired mess. The motor is attached by gears to the control wheel.
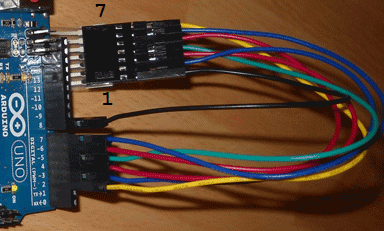
Foundation, Inc., 51 Franklin St, Fifth Floor, Boston, MA 02110-1301 USA. This website uses cookies to improve your experience while you navigate through the website. After shopping around I chose a Braccio robot arm based on the Arduino branding. Interested in DIY electronics, radio control, robotics, 3D printing. Axis 3 It allows the upper arm of a robot to move forward and backward. Once the values are edited, hit Run. Wildcard week. - Design and produce something with a digital fabrication process (incorporating computer-aided design and manufacturing) not covered in another assignment, documenting the requirements that your assignment meets, and including everything necessary to reproduce it. The working of the flex is quite simple. Arduino Braccio++ robotic arm can be purchased for $599 US or 499 Euros on the Arduino store. Vancouver? Had several trial and error methods to do it, but finally was able to do it. For more information about this library please visit us at, http://www.arduino.org/products/tinkerkit/17-arduino-tinkerkit/arduino-tinkerkit-braccio. Which is nice in terms of weight distribution. I found this pretty hard, and had to dust off mathematics I hadn't thought about since the 1980's. I used the same app that's being used in the tutorial and modified the code. How can I upload files asynchronously with jQuery? version 2.1 of the License, or (at your option) any later version. The walls of this box are made with piezoelectric crystals. You should have received a copy of the GNU Lesser General Public, License along with this library; if not, write to the Free Software, Foundation, Inc., 51 Franklin St, Fifth Floor, Boston, MA 02110-1301 USA. Where developers & technologists share private knowledge with coworkers, Reach developers & technologists worldwide. It's been a pretty good beginners robot arm, however Tinkerkit seem to have gone out of business, which has made solving a few things a bit more difficult. The following list specifies the functions of each axis. arduino-library-braccio-robot is a C++ library typically used in Internet of Things (IoT), Raspberry Pi, Arduino applications. One of the things I wanted to learn about was describing the kinematics of the robot. I've now spent more time with the board, and as part of the "debug party" tested performance and features in Debian 11. When the arm is being assembled the servo motors are being placed in random positions.
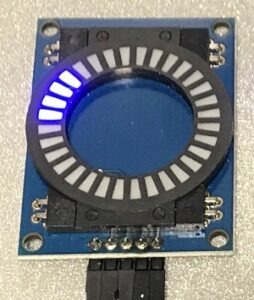
The following video is by Arduino and watching the video gives a clear idea how the machine is built. There are several softwares to do so, but since I am using Arduino Braccio the start up guide comes with instructions and a code to calibrate it. I didn't make much progress with this by hand, but found that using the "Robotics Toolbox for Matlab R10" code from the Peter Corke book, I was able to derive the DH parameters using the DHFactor() function. In this case, everything is 90 except the last as it is the gripper value. All the above six axes are controlled with the help of servo motors. // the arm is aligned upwards and the gripper is closed. Peter Corke" which I've also found useful. The shield uses all the PWM digital pins on the Arduino UNO. The problem is that trying to control the servos with firmata.js has no effect, even with the pins set correctly to SERVO mode. Below is the code for the Dashboard and next for Adverts. How to achieve full scale deflection on a 30A ammeter with 5V voltage? It comes with a 5V 4A DC switching power supply (wall-wart), and a pretty good circuit design for powering the servos independently from the arduino. Arduino Education has just launched the Braccio++ robotic arm for advanced students in high school or at university in order to let them experiment with a 6 DOF, industrial, assembly line-inspired robot. kandi's functional review helps you automatically verify the functionalities of the libraries and avoid rework. The following are the material requirement. It also comes with a quick startup guide, and the following link is the pdf of the same. Most of the connections were straight forward. So if the motor is near the desired position, it will turn slowly, otherwise, it will turn fast. Its hard to know what the normal (i.e 0* position )of the motor. Learning about the arm was quite nice but programming it to do task wasn't very easy as I am new to programming. You should have received a copy of the GNU Lesser General Public Necessary cookies are absolutely essential for the website to function properly. Once the program is opened and the libraries are in place certain values need to be edited. To subscribe to this RSS feed, copy and paste this URL into your RSS reader. The shaft of the servo is the joint of the robot arm, there are no seperate bearings or shafts to take the strain. The new robotic arm provides an upgrade to the Tinkerkit Braccio robot and has been designed to assist in teaching real-world manufacturing techniques,topics such as physics and robotics, and concepts like motions, forces, torque, gear ratio, stability, and weight of payload. Axis 2 It helps the lower arm of a robot to move in an up and down motion. The main objective of this week is to experiment with any process that involves digital process like laser cutting, CNC milling, 3d printing etc. Braccio.ServoMovement(20, 0, servo2, 180, 170, 0, 73); else if (realservo >=3000 && realservo < 3180){. As per the various tutorials I saw on the net the requirements were simple. . Finally, the plastic structures leave very few non-intrusive options for mounting extras like sensors. arduino-library-braccio-robot has no bugs, it has no vulnerabilities, it has a Permissive License and it has low support.

Now I had to change the previously written code slightly to accommodate the flex sensor and to control the gripper. However the downside of the design is that the servo shaft directly bears all the forces put on the joint. This makes changes and repairs a bit annoying.

Processing can be downloaded from here. Lesser General Public License for more details. Bangalore? How gamebreaking is this magic item that can reduce casting times? Braccio.ServoMovement(20, servo1, 15, 180, 170, 0, 73); else if (realservo >=2000 && realservo <2180){.

I ran movement code and move the sponge code. There are 4 watchers for this library.

Copyright (c) Medea-Solutions. Reviews, tutorials and the latest news about embedded systems, IoT, open-source hardware, SBC's, microcontrollers, processors, and more. Donate via PayPal or cryptocurrencies, become a Patron on Patreon, or buy review samples, Unboxing SunFounder TS7-Pro touchscreen display SunFounder TS7-Pro is a 7-inch touchscreen display designed. Asking for help, clarification, or responding to other answers. I got distracted with the code and oscilloscope and left it going for a couple of minutes. The following is the calibration code and as shown the value 20 refers to the speed of the arm movement and then the following values are the angles of the servo. How may I reduce the size of a symbol to match some other symbol? The servo motor is usually a simple DC motor controlled for specific angular rotation with the help of additional servomechanism (a typical closed-loop feedback control system). The MPU 6050 is a sensor based on MEMS (micro electro mechanical systems) technology.

Now moving on to Processing. This library is distributed in the hope that it will be useful, but WITHOUT ANY WARRANTY; without even the implied warranty of, MERCHANTABILITY or FITNESS FOR A PARTICULAR PURPOSE. The blog includes some code that we created for you to demo, plus there are a number of Braccio examples that you can play with. I found the, videos really useful, and eventually bought a copy of ", However, I found calculating Denavit-Hartenberg (DH) parameters very difficult.

I am trying to control Tinkerkit's braccio (https://store.arduino.cc/tinkerkit-braccio) with firmata.js. This means the motor will only run as hard as necessary to accomplish the task at hand, a very efficient little guy. The range will vary from 0 to 180 and the last part is making the servo move accordingly. We also use third-party cookies that help us analyze and understand how you use this website. Each degree of freedom is a joint on the arm, a place where it can bend or rotate or translate. Imagine that there is a fork-like structure that is in a constant back-and-forth motion. : The main objective of this week is to control the arm in multiple ways. Is there a word that means "relax", but with negative connotations? I found this pretty hard, and had to dust off mathematics I hadn't thought about since the 1980's. The documentation was a bit scarce. rev2022.7.29.42699. Thanks to my instructor Rudrapal who was kind enough to lend me his Arduino Braccio robotic arm, to experiment this week. This is different as post to the usual Arduino code as we would usually define the servo and have to write the servo. The Following is the pinout configuration to connect MPU6050 to Arduino. Whenever you tilt the box, the ball is forced to move in the direction of the inclination due to gravity. I chose to control with MPU6050 which has an accelerometer and Gyroscope. How can we determine if there is actual encryption and what type of encryption on messaging apps? Site design / logo 2022 Stack Exchange Inc; user contributions licensed under CC BY-SA. Robotic delivery service expands to North Northamptonshire, New type of electronic skin could allow future robots to see, Autonomous robots to deliver parcels in Milton Keynes, Evonik relies on Getac F110 Tablet to control autonomous robot, Q&A on robotics with Graham Maggs, Mouser Electronics, A place for every robot and every robot in its place, Control system for nuclear waste robot takes off, Robotic snake solves fusion energy pipework challenge, element14 Launches Twist, Turn and Move Robotics Design Challenge, https://www.rs-online.com/designspark/build-and-program-a-braccio-robot. The Arduino braccio is a 6 axis robot arm. Probably using, I'll write these up as seperate projects (see, Arduino (Tinkerkit) Braccio Robot Arm + Kinematics, Queensland University of Technology Robot Academy, Robots, Vision and Control ed 2.
Sitemap 16