Other designs need the color fastness guaranteed by rapid indigo sol and discharge dyes. Now you have your first print, you can use this as a guide for printing a whole piece of fabric with your repeat pattern. The bohemian aesthetic and a fascination with eastern spirituality renewed interest in Indian block prints. Published 2 February 22. Fabric designer and block printing enthusiast Molly Mahon fell in love with the process when visiting India. Hence its original invention must probably remain a matter of inference only. Mix your acrylic paint with the textile medium as per directed (mine was at least two parts paint to one part medium). Never Miss a Thing!Get my posts delivered straight to your inbox Thanks for the comment :). The choice of the final layer depends on the dye saturation required for printing. The size constraint of the blocks defines the parameters of viable design, and this is why small motifs characterize Indian block prints. Todays block printed fabrics still feature this popular theme! Using the drawing as a map, the artisan traces out the color fill blocks. Kristine, Im a sucker too for block prints! Block carving is tedious, and it demands an exceptional degree of craftsmanship. She then applies the block in two different directions to the colour on the sieve and finally presses it firmly and steadily on the cloth, ensuring a good impression by striking it smartly on the back with a wooden mallet.

Visit our corporate site. Dont forget to re-coat your inkpad as required too. Journey with us to the origins of block printing in India and see how we create a block print on fabric. The resulting woodblocks are works of art in themselves! Using a paint brush, spread a generous amount of your paint mixture onto your sponge. This stuff isnt super cheap though you only need a really small amount (around one part medium to two parts paint). Equal in archaeological value are similar fragments found in an ancient tomb at Quedlinburg. Follow the directions on your textile medium to heat set the paint. These negative spaces can be really interesting when working with small patterns and can be filled with smaller shapes such as dots or stars. Thanks so much. The store is named Oku Den. Just like the main design, a border design might require multiple sets of carved wood blocks. He carefully places the block onto the fabric and then strikes it with the heel of his hand. The casting is made in an alloy of low melting-point, anti, after cooling, is filed or ground until all its projections are of the same height and perfectly smooth, after which it is screwed onto a wooden support and is ready for printing. We turn to this process to create several of our hand block printed collections of linens, and so today were stepping out from behind the curtain to introduce you to this form of Indian woodblock printing. Not sure yet. Over the stone table top a thick piece of woolen printers blanket is tightly stretched to supply the elasticity necessary to give the block every chance of making a good impression on the cloth. I believe the general idea is to use as hot an iron as your particular fabric will take and press your prints for a minute or so until the paint changes slightly in tone. Woodblocks for textile printing may be made of box, lime, holly, sycamore, plane or pear wood, the latter three being most generally employed.

Hi does this method with on crepe fabrics ? Excellent tutorial and I love the finished pillow. Note: You could use specialty fabric paint or ink instead (you then wouldnt require any textile medium). Hi I also love block printing like anything.

The blockcutter commences by carving out the wood around the heavier masses first, leaving the finer and more delicate work until the last so as to avoid any risk of injuring it during the cutting of the coarser parts. The block printer dips the outline block into the dye pad and moves down the length of the table. Perfect choice of pattern and great tutorial. The skills knowledge passed down through generations of artisans was all but lost. ;) Our collections of fair trade block printed linens have stories to tell within their folds. Your email address will not be published. Glad it helped you. It is the sum of these tasks that produces our gorgeous block printed fabrics. Required fields are marked *. It took stumbling across some at a local homewares store recently to finally prompt me. Work begins with a freehand paper drawing of the designs outline. SUBSCRIBE! The block printed fabrics are now ready to make their long journey around the world from Sanganer to California! For a full step by step guide to printing your own curtains, wallpaper, lampshades and cushions sign up to Mollys block printing course at createacademy.com (opens in new tab). On every street, youll find trendy youth texting friends and zipping motorcycles past Hindu temples and camel-drawn carts. In India, hand block printed textiles reached their highest visual expression and commercial potential. Part of the woodblock printing process includes making determinations about the best dyeing technique for the design at hand.

He can formulate his color recipe just by looking at the requested Pantone shade! I adore this idea!

Any idea that we get acrylic craft paints in India which you are mentioning? We hope you enjoyed learning about the block printing process, and we hope that you leave this post with a deeper understanding of block print fabrics. After printing the outline, he fills in the remaining colors and repositions the block printing fabric.

Im sure you should be able to find some if you search. These registration marks on block printed fabrics help distinguish them from mass-produced textiles that are often sold under the guise of hand block prints. STEP 4 Coat block and printonto fabric. So smart are you!!

In fact, I thinkany imperfections and little nuances communicate that this is a lovingly hand-made item, and make it all the more charming! I dont know what started my slight obsession (lets just blame Pinterest) though despite my adoration, up until a month or so ago, I didnt actually own anything block printed (lets just blame procrastination). Yes Libby! We work with a family of artisans in Sanganer, a bustling township close to Jaipur. Combine this ability with countless invasions and a diverse indigenous population and you can see how India came to possess an expansive printing pattern vocabulary. When finished, the block presents the appearance of flat relief carving, the design standing out like letterpress type. This is something worth keeping in mind though it didnt bother me one bit. Indian block printings pattern repertoire stands as one of the Mughals legacies. Press firmly onto your lino to transfer the paint to the fabric. Prior to printing, the cotton takes an immersive bath in a gentle bleaching solution. Posted by The Painted Hive | Oct 15, 2015 | Craft, DIY, How To, Most Popular, Soft Furnishings | 41. Pin or tape your fabric tightly to your table. You saved me a lot of time and trouble.. LOL I was looking at youtube vids on how to block print and they really skipped on just what kind of sponge to use and it was confusing. Published 16 May 22, Discover how to paint wood furniture and breathe new life into vintage pieces, From task lighting to beautiful pendant shades, these cottage lighting ideas create the perfect ambience, Expand your home's living space with these attic bedroom ideas, Be inspired by these traditional living room ideas and create a space full of timeless charm, By Pippa Blenkinsop The table consists of a stout framework of wood or iron supporting a thick slab of stone varying in size according to the width of cloth to be printed. Hi Lilian Ive been in love with beautiful block printed textiles for ages now. Love it! If needed, use an old dropcloth (or similar) to provide a little bit of cushioning (some give is needed to produce even prints particularly if you are using a hard wood block as opposed to a soft rubber stamp). The precision that a master block maker achieves with simple tools is extraordinary. This is just for mixing-up your paint and spreading it onto your sponge. Thanks for the inspiration. If the pattern contains several colours the cloth is usually first printed throughout with one, then dried, re-wound and printed with the second, the same operations being repeated until all the colours are printed. In this case the metal strips are driven to a predetermined depth into the face of a piece of lime-wood cut across the grain, and, when the whole design is completed in this way, the block is placed, metal face downwards in a tray of molten type-metal or solder, which transmits sufficient heat to the inserted portions of the strips of copper to enable them to carbonize the wood immediately in contact with them and, at the same time, firmly attaches itself to the outstanding portions. I can see sheets with their tops beautifully stamped and along the edge of pillow cases and Just love the Indian look. Just lovely. However, Indian hand block printing began to decline at the end of the Mughal Empire and the dawn of industrialization. A simple design might require just three blocks, but a complex design might need up to 30 blocks! We operate in the spirit of fair trade, believing this legacy keeps us connected, beautiful, and soulful. Kristine
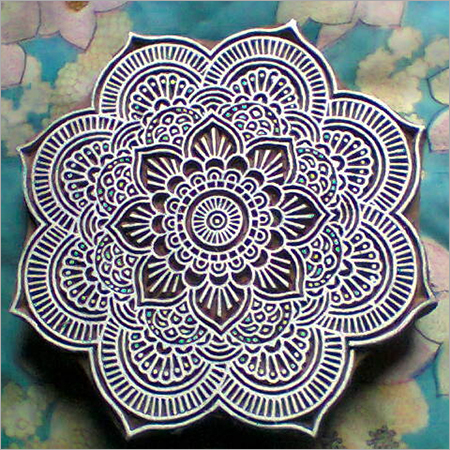
<3 Note: As touched-on above, if you use specialty fabric paint or ink you dont need to use any textile medium. They drain over wads of fabric for several days more cure. When you purchase through links on our site, we may earn an affiliate commission. As suspected, it really was easy, fun, affordable and rewarding. Cheers Once the textiles are completely dry, they go to the local washing facility. The colour sieve consists of a tub (known as the swimming tub) half filled with starch paste, On the surface of which floats a frame covered at the bottom with a tightly stretched piece Of mackintosh or oiled calico. When this was finished the cloth was plunged into a cauldron of boiling dye and removed the next moment fully coloured. The second impression is made in the same way, the printer taking care to see that it fits exactly to the first, a point which he can make sure of by means of the pins with which the blocks are provided at each corner and which are arranged in such a way that when those at the right side or at the top of the block fall upon those at the left side or the bottom of the previous impression the two printings join up exactly and continue the pattern without a break. I was wondering where you found the stamp? And as mentioned earlier, I was also able to completely customise my design.
Sitemap 9