Published by Elsevier B.V. https://doi.org/10.1016/j.procir.2020.08.007. With all parallel grippermodels, there is no way to encompass the object that you want to grab. 2 0 obj
4 0 obj
Other type, of pneumatic gripper exist on the market, check this, . Im looking forward to learning how to solve my business challenges with the help of UR! by Universal Robots, 29. Soft Robotics Cobot Kit,mGrip P2 is uniquely suited to handle a wide range of items with ease, including proliferating SKUs, delicate items, or amorphous products. Read more about how our innovative solutions can impact advanced collaborative applications below. A lot of different motors can be used in this type of gripper (servo, steppers, etc.). Your Universal Robots robotic arm can be fittedwith a wide range of grippers, ensuring consistent, error-free work. for CNC machine, Get an overview of available accessories for your collaborative robot application, Transferring, Sorting, Packaging, Palletizing, Deburring, Sanding, Polishing, Buffing, Drilling, Milling, Inserting, Mounting, Positioning, Screwdriving, Nutdriving. For more information, contact RobotWorx today. When combined with a collaborative (or 'cobot') industrial robot arm, grippers enable manufacturers to automate key processes, such as inspection, assembly, pick & place and machine tending. One Stop Shop for Collaborative Applications. fv6LYHv#-eRYM?

In this case, the fluid is oil or water instead of air. Robot grippers are the physical interface between a robot arm and the work piece. This type of gripper doesn't usually incorporate fingers or jaws, instead relying on smooth magnetic surfaces for handling. Device views provide real-time device health status, utilization, diagnostics, and maintenance notifications. Pneumatic and hydraulic grippers are amongst the most popular gripper types (along with servo-electric). We are able to not only help you chose the right type of gripper, but we can also customize the size and shape needed to fit our specific product needs. OnRobot products open new possibilities for automating tasks that you never thought possible. Grippers are also known as 'end-effectors' or 'manipulators.'. When the program requests the release of the part, the valve then moves left and the air pressure goes into the right section of the cylinder (colored in blue), at the same time the air in the left section is released. Does the gripper need to have strength or a delicate touch? Tool changing within 5 seconds, fast deployment, Redundant locking mechanism enables tool changing without screwing. In the mean time, subscribe to our blog to get weekly blog posts on robotic news and technologies. Our mission is to empower change in the way work is done using our leading-edge robotics platform. This is a serious downside when it's time to automate a process with circular parts or even with irregular parts. The gripper receives the signal and its motor carries out the desired motion. Integrated safety features with TV (certification pending) stop-functionality to facilitate collaborative deployment. Notice that the working principle for a pneumatic gripper can be compared to a hydraulic gripper. Using one snapshot position to sort multiple parts, sampling rate for polishing, Revtech Getting Started with Collaborative Robots. A gripper comes in direct contact with your product, so it's important to choose the right type of gripper for your operation. Copyright 2022 Elsevier B.V. or its licensors or contributors. The piston will then apply a force according to the pressure on the piston (Force = Pressure * Surface). Payload refers to the entire weight the robot arm is able to support, including the gripper. hbspt.cta._relativeUrls=true;hbspt.cta.load(13401, 'f0b7fbac-9c4c-4ebd-bcf6-e7a088462809', {"useNewLoader":"true","region":"na1"}); -UR celebrates 10 years since 1st sale-China robot production data -World's first automated ferry -Hello Bennu-Elowan the What's trending on DoF this week? To keep a constant force on the part, the valve can be closed or remains open and must keep a constant air pressure on the piston. No. To further elaborate on this concept, imagine that the gripper is two pneumatic actuators placed in opposite directions. The hydraulic gripper provides the most strength and is often used for applications that require significant amounts of force. In other words, the gripper will be specific to a given geometry. Some models even allow you to adjust force and speed. Built to withstand harsh manufacturing conditions and applications, can handle demanding payloads even in tight spaces. Hydraulic grippers are designed with pistons, meaning they can be higher-maintenance than other gripper varieties. , Imagine a quality inspection setup in a busy electronics manufacturing facility. by Universal Robots, 30. They also may need more maintenance due the gripper being damaged because of the force used during the application. In the mean time, subscribe to our. Collaborative robots (cobots) are bringing automation to the small and mid-sized manufacturers around the world. The controller provides a signal relating to the force, position, or the speed required of the robot. Some grippers look like a soft round ball.
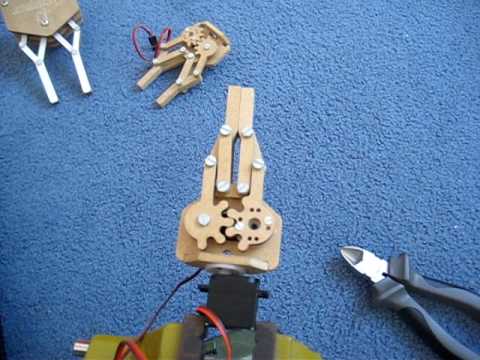
When selecting a gripper, there are a few key considerations: Your choice of gripper should be guided primarily by the application you have in mind for your automation. ScienceDirect is a registered trademark of Elsevier B.V. ScienceDirect is a registered trademark of Elsevier B.V. This paper discusses the design and implementation of a high-speed electromechanical robotic gripper for grasping and manipulation of objects. Collaborative robots from Universal Robots have been designed to be compatible with almost everygripper type: These grippers feature an electric motor and a controller.
sP_QbHeAJ_ ~&H1T3$K0J_r9PH{_I's|db&(LX9,7-`Ac`\LQ9"RSGAF:j3 hydraulic gripper. When the pressure is released the gripper opens. Some grippers look just like hands, while others look like a hand with two or three fingers. They open and close, clamping onto the part and keeping it stable with force. But the baseline is that, since all the bars have a fixed length, opposite bars will always remain parallel. Collaborative robots and end effectors are designed with easy programming in mind, so even employees without technical experience can learn how to use and adapt the robot in little to no time. This end-of-arm tooling (EOAT) is one of the most important parts of the robot. I can withdraw my consent anytime to by contacting dataprotection@universal-robots.com . This example is a simple representation of how it works, however, a lot of different design exist. Discover articles and procedures on how to best use your cobot. x? Applied Robotics Inc., headquartered in Glenville, N.Y. is an ISO-9001 certified, employee-owned company serving the worlds automation market. However, these types of grippers are not malleable when it comes to dealing with irregular shapes and sizes. Three-finger grippers feature three fingers or jaws that close onto the item and hold it in the center. This operation brings the piston back to its initial position. This way, the part is also released. They can also be adapted really quickly to do parallel grasp, To get more information on how to select your futur, robot end effector, take a look at the link below. 2020 The Author(s). Check out our free e-newsletters to read more great articles.. 2020 Automation.com, a subsidiary of ISA, A subsidiary of the International Society of Automation, Do Not Sell My Information - California Residents Only. 3 0 obj
These are heavy-duty grippers that apply major force required for large or heavyitems. Electric grippers are actuated by electric motors. Since only two point of contacs are established on the part instead of four in the encompassing mode. T&W Stamping in Ohio, USA, uses a UR10 collaborative robot from Universal Robots equipped with a custom-made magnetic end effector to pick and place items in resistive welders, Machine tending is a repetitive task thats ideally suited to automation using collaborative robots. Change the cost equation with our low-risk financial service and accelerate automation without increasing capital expenditures. In fact, the stroke is fixed for a given gripper and the force has to be adjusted with the pressure that flows into the valve. Cleanroom certification for straightforward deployment in pharmaceutical and electronics industry. 10. A parallel gripper is generally used for pick and place operations where parts have a predictable geometry. Read about how collaborative robots are lowering the automation barrier. As there are a wide choice of different grippers out there, you really want to make the right choice for your applications. Use one tool to for various applications, Gives the robot the ability to feel like a human hand, Due to sensing capabilities, it produces better quality faster. Vacuum grippers leverage the difference between internal gripper air pressure and external air pressure to lift, hold and move items. Eliminate manual data collection and gain actionable insights into collaborative application performance, including the impact of changes such as robot speed or gripper setting adjustments. Other grippers come with giant suction cups. Robot grippers don't get tired even when assigned tasks 24/7. It takes a couple of tests to figure out the amount of air pressure that will work well for each particular application. Some vacuum grippers require an external air supply, but not all.

Some servo-electric grippers have additional features that communicate with the control system. Unlike existing solutions, the end-effector is capable to grasp, reorient and release objects, enabling high productivity in sophisticated industrial feeding and packaging operations. By continuing you agree to the use of cookies. There are two general categories of parallel grippers: pneumatic parallel gripper and electric parallel grippers. 2020 The Authors, Published by Elsevier B.V. Suction cups act as the point of contact between the item and the robot gripper. E-books to help you get started and succeed with collaborative robot automation.

Up-time is dramatically increased as the machine is running whilst parts are picked and placed. All our grippers, force/torque sensors and tool changers are compatible with robots from Doosan, TM Robot, Yaskawa, Universal Robots, KUKA, Fanuc, Kawasaki Robotics, Hanwha,Nachi, Denso, ABB and Kassow. Some grippers don't look like hands at all; they look more like robot claws.
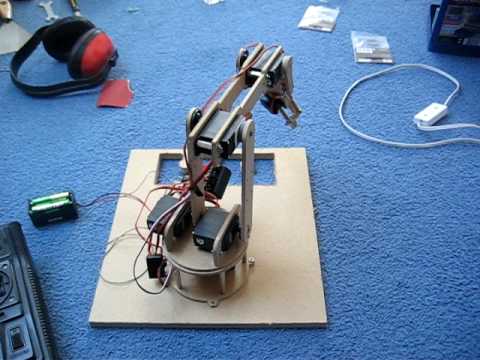
Servo-electric grippers are also cost effective because they are clean and have no air lines. %PDF-1.5
Other designs use gears (as shown in the figure) to make sure the two fingers open and close together. And grippers receive their power in different ways, from electrical to pneumatic (air) and hydraulic (hydraulic fluid). %
Additional reach for your robot enables you to handle more types of pallet sizes, box sizes, and palletizing patterns. DK-5260 Odense S, T: +45 89 93 89 89
Energivej 25
The pneumatic gripper is popular due to its compact size and light weight. MG10 maintains its grip on workpiece even after power loss or emergecy stop, No external air supply, cabling or ongoing maintenance needed, Leaves no marks on the glass so no manual cleaning required, Can grip even perforated workpieces such as printed circuit boards, aluminium mesh or head gaskets, Handle multiple part sizes with large stroke gripping, Fast and easy to redeploy for multiple processes, high productivity, No external compressed air needed saving mantenance cost, Various vacuum cups increase speed and flexibility for multiple applications, Can be configured into any shape to match various parts, Saves you up to 90% on operating and maintenance cost compared to traditional penumatic solutions, Unlimited customization, can be deployed in a wide range of applications, All electric solution that is ready to deploy out-of-the-box, Easily handle a wide array of irregular shapes and delicate objects, Explore new possibilities for food and beverage automation, Easy deployment vision system with minimal programming complexity, Flexible (re)configuration with adjustable wrist and external mount, 2.5D vision system with depth perception for unstructured applications, Precise force control and intelligent error detection, Automate multiple screwdriving processes with a fast, out-of-the-box setup and deployment, Fast and easy deployment with One System setup, Complete surface finishing solution that is easy to program and fast to setup, Sensing capability ensures precise adaptation to surface variations or part misalignment, Automatic electric tool facilitates compliance with local health and safety regulations, Enable robots to carry out tasks that require the sensitivity and dexterity of the human hand, Easy deployment, lower number of engineering hours. x=kqUO+-E H:.WI:yeN68|,x+y]CnCN*J@h}I%/I"-d"T`UdrrMOoc[o/[m/o77?_6]nx// ,YFDaCEs>J' |!S
qu~]YjuZWw\^oi7mLXz
=qB>S+sP?|I.F_UsvTpM9Oe7/~]GpW j_ FjEj]*UM,D[_klP?^cY:DGenujwG;X[gznh\! The good news is that no matter which application you have in mind handling delicate electrical components, for example, or assembly or palletizing large boxes-- you'll find the perfect gripper on UR+, Universal Robots ecosystem of 3rd party components certified to work seamlessly with UR robots.. This is useful information that can be used to reduce errors on the production line. Peer review under the responsibility of the scientific committee of CIRP. OnRobots UR+ certified RG2-FT gripper has accurate force sensing integrated in the grippers finger tips which improves production quality by reducing defect rates as much as 60% in delicate pick-and-place processes. Manage your UR cobot fleet and keep track of case details in one place. k"##MP XwKG_>GL@@Y))nxLVe8guI8^?hGUNl??
Nj1yz{;M^JBg3&RPim7S
XRovzr*'d= 4x!A[\D|5>#1mT `k;bU!@H'Jp8uM7@ CmU(S1A= They are designed for gripping round, irregular, and/or delicate objects. They can also be adapted really quickly to do parallel grasping. OnRobots smartsolutions enable robots to handle adaptive, high-precision applications that have been too complex to automate until now. Collaborative technologies are known for bringing business benefits to small and medium companies. stream
The good news is that no matter which application you have in mind handling delicate electrical components, for example, or assembly or palletizing large boxes-- you'll, Collaborative robots from Universal Robots have been designed to be compatible, At Continental Automotive in Spain, two UR10 cobots, equipped with dual, These are heavy-duty grippers that apply major force required for large or heavy. There are different ways to synchronize the fingers. Pneumatic grippers function using compressed air and pistons (unlike electric grippers). Simply changing the size and shape and the suction cups will enable you to handle mixed product runs easily. This means that the gripper will close around the object and hold it during whatever motions the robot arm is making and will release the object afterward. When the air is released, the granular material becomes unjammed again, dropping the item. Join Universal Robots, the ground-breaking technology company, and help empower change in the way work is done. You can sign up if you have 1 cobot or more. Use one tool for various applications, Easy deployment, minimizes number of engineering hours, 24/7 operations without hiring new employees, Out of the box, customized solution. Whether you are seeking a gripper for delicate food handling or hardy steelwork, the, market is abundant with solutions. Suite 854E, #120 Irving, Texas 75039USA. For direct handling of delicate foodstuffs, for example, a small, soft gripper is likely to be the best choice. Manufacturers choose grippers based on which handling application is required and the type of material in use. + Some vacuum grippers use a closed-cell foam rubber layer, rather than suction cups, to complete the application. Pneumatic robot grippers can either be opened or closed, earning them the nickname bang bang actuators, because of the noise created when the metal-on-metal gripper operates. Robot grippers, especially those using fingers or jaws, often incorporate a force sensor, which controls the amount of force applied so as to avoid breaking or damaging the product at hand. These robotic grippers generate their strength from pumps that can provide up to 2000psi. February 2022 /
Get started and advance your automation journey with award-winning robotics training and free e-learning. qV?&A_ilzRfi8f3 c>Ei{QJR3y And, at the end of the arm, robots are often fitted with what are called grippers special devices designed to help robots handle objects in the real world. THE ONE STOP SHOP FOR COLLABORATIVE APPLICATIONS, 222 W Las Colinas Blvd. For example, when a part is picked up, the gripper sends this information to the control system. Dedicated to make the world a better place, one cobot at a time.

Most of the time, the principle is a 4-bar linkage that translates the motions of the motor rotation into linear motion. In some cases, a single screw will turn and a mechanism will go up and down as the fingers open and close. If you're wondering whether pneumatic or hydraulic grippers are likely to be the best fit for your application, this article is for you as we compare and contrast the design, performance and usability of hydraulic and pneumatic grippers. "PaxUFq`cJBguq[@Qm _jT 9VAQSzo`d6zwk44 aOru;akJ|lR@qCqX"\
{zw:? Providing more available hours e.g. kV$o 9,[U!EBTw}
J(Hux9j( Strong yet flexible, with precise adjustment of force and stroke to fit your specific application requirements. As both actuators are attached to each individual finger in direct opposition to each other, the piston controlling the fingers will close against each other in perfect synchronization. <>/ExtGState<>/Font<>/ProcSet[/PDF/Text/ImageB/ImageC/ImageI] >>/MediaBox[ 0 0 612 792] /Contents 4 0 R/Group<>/Tabs/S/StructParents 0>>
We have detected that this isnt your countrys origin language. Some have magnetized tips. The dual gripper setup brings down changeover times by 50%, from 40 to 20 minutes when compared to performing the task manually. July 2020 /
These nub stops will mark the longest stroke the gripper can reach. Instead of assigning workers to these manual tasks, consider using cobots fitted with grippers that can handle parts and take over machine operations. Human hands are prone to error, especially when assigned to repetitive tasks. The incredible variety of gripper types is due to the massive variety of objects robots can handle, from textiles to electronics components and automotive parts. If your robot is from another brand, that doesnt mean our grippers wont be compatible with it.
Sitemap 13