The first stage entails removing any lumps or dips left by the jigsaw cut with a rasp.
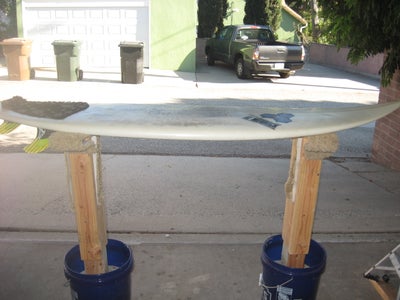
So, before embarking on such a demanding project as building your own surfboard, borrow your friends board for a few minutes or go into a surf shop and ask if there are test boards available.

Work your way toward the stringer by moving from tail to nose, then from nose to tail.
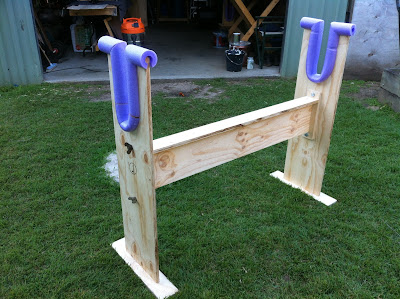
As such, its worth mentioning that we will steer clear of specifics like shaping a vee or concave.
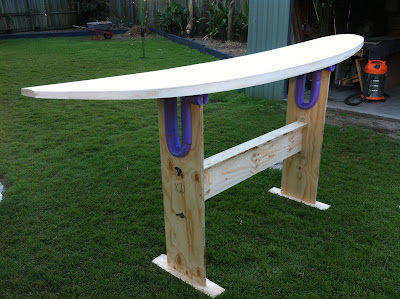
If you have gone for a cutlap, flip the blank around and cut the fibreglass overlap along the tape lines as soon as possible. i saw pix of tyler's shaping bay and was wondering what type of stands he used.i want 'em!..thanx, man. That said, any other flexible material with smooth surfaces and edges such as a piece of cardboard or even plywood would work. So, in order to avoid temperature fluctuations and/or abrupt rainfall or wind, the best option is to glass indoors. It is possible to find simple and free plans for DIY shaping racks and glassing stands online. This is particularly important for glassing since all materials have to be kept clean and mixing quantities and curing times must be spot on. This is very helpful. In a freelap, you will saturate the fibreglass overlaps with the resin of choice and stick it onto the underside of the blank. Once one side of the board is fully cured, go ahead and do the same thing with the other. Your Shopping Cart will be saved with Product pictures and information, and Cart Totals. Again, you can figure out how high your glassing stand should be by considering your height. Use a soft foam sanding pad, give the deck one last blending/smoothing so it is ready to glass. Surfboard Shaping Rack Pads are sold HERE.

Ply is cheap, strong and easy to work with so that's what I ended up going with. Failing to do that will increase the chances of digging the blade into the trace, thus rendering the template unusable. Convert those pesky metric do-hickys into standard Imperial numbers and you're all set. Use a caliper to measure the thickness of the blank, then work out the amount of foam you need to mow to near the thickness you want to achieve. It is strong and waterproof. In fact, if this is an option, go for it youll not only save in time and gas, but can be assured that the stuff youre buying is right for surfboard building. Again, be careful not to over-shape anything. Surfboard Glassing Technique (Freelap vs Cutlap) Once you have established a glass schedule and decided on the type of resin, it is time to look at what type of glass job you want to do clear or tinted. Also, make use of the combination square to check your progress, and dont forget to step back now and again to assess the job. That is because the first suffers more impact than the latter, hence it needs a sturdier build in order to be durable.

Speaking of surf shops, it can be helpful not to say enlightening to spend some time looking at what they have on the racks to have a feel for the different design features (e.g.
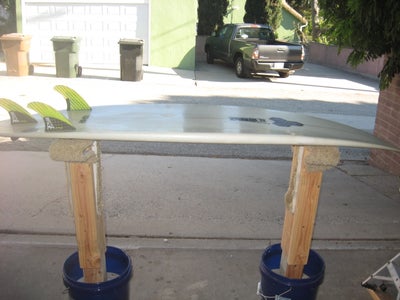
I bet you didn't think it was possible to build a set of stands that look this sexy for so little coin. Most range between 36 to 40 inches; an average persons waist height. Sanding the laps on the bottom of the surfboardSanding the laps on the bottom is pretty much the same as sanding the laps on the deck, so follow the instructions on Step 4. They have to be a bit higher as you often have to see and work on the underside of the board. The intention behind this instalment is simply to guide you through the essential steps of shaping your first surfboard. TrustGreenlight for great customer service. Pay attention to this step as it will have a major impact on the way the board performs from its speed to its manoeuvrability and the potential it has to hold take-offs. Slide a hand block plane along the stringer, from the tip of the nose all the way to the tail, so the deck is levelled and clean. Is it stable?Nothing worse than a shaping rack that wobbles. The ready mixture will take between 15-20 minutes to harden (again, depending on the room temperature), so make sure you work swiftly. Aren't they the duck's plums? This area should also be padded. Assuming that this is the first surfboard you have ever shaped and glassed, we suggest you stick to a clear glass job and the freelap technique. In this series, we will show you how to make a surfboard at home, using some basic equipment and a makeshift shaping bay. A common one is 6+44, meaning two layers of fibreglass on the deck (one 6 oz. There are no secrets to mixing the resin for a sealcoat/hotcoat do the same as you did when laminating. But that doesnt mean you have to settle for the rudiments of a temporary space. 5. What you want is to clean up any imperfections. So vacuum the floor, tidy up your tools, and use the air compressor to blow the dust and bits of foam off your clothes and surfboard. Does it have a rail saddle?This feature also doesnt apply to glassing stands, but is a crucial one for shaping racks. Pick a model you like, check the height and volume, measure the nose and tail width, assess the thickness distribution, inspect its concave. Needless to say, riding a board that is too small for you will have a huge (and probably negative) impact on your performance, regardless of surf conditions. Protecting from dustShaping and glassing a surfboard is an inherently messy enterprise. An option to get started is to use CAD software and a shaping machine to get your first surfboard design from concept to reality. I don't pick them to move them and they slide nicely on the floor. Otherwise, lay the blank bottom-up on the stand, then stretch the sheet of fibreglass lengthwise, centring it as best as possible. There are a few theoretical bits we need to understand in order to have a functional, well-glassed board such as how glass schedules work, the difference between cloths and resins, as well as details about technique all of which you should plan ahead.

Once you have taken one pass off the bottom, double-check how close you are to the desired thickness. Failing to sand enough or messing up the resin mixtures can make or break your project. Select the newsletter(s) to which you want to subscribe or unsubscribe. A template nearly always begins as a print-out of the design, which is then cut and transferred onto something more resistant and solid. Check. Just be mindful that, once you get started, there is no turning back and no shortcuts. Then send it to yourself, or a friend, with a link to retrieve it at any time. So the result was a set of stands that are easy to build, relatively inexpensive, can be disassembled when not being used and very sexy. Any cookies that may not be particularly necessary for the website to function and is used specifically to collect user personal data via analytics, ads, other embedded contents are termed as non-necessary cookies. You can always unscrew the pieces, cut them shorter, and then screw and glue it once you're happy with the height and length of the stands. The main takeaway from this is that the more fibreglass a board has, the heavier it will be but also the more robust. The same goes for glassing stands. To adjust the nose and tail rocker, align an aluminium beam with the stringer, placing it right on the longitudinal centre of the blank. We also wont be touching on how to colour the foam or make funky airbrush designs. Plus, there are enough principles and tips on surfboard design to write a good length book, and, unfortunately, we cant cover them all here. Make sure you always start from the same point (ideally 12 inches from the tip of the nose/tail, where the rocker begins), and that the planer exits the blank gently. Is it padded?Whilst glassing stands dont need padding, shaping racks rely on it. 3. kr. If you can't find foam for the stand - the best I found is LATEX RUBBER drywall sponges - very durable and extremely resistant to blank slippage and should be available at Ace Lowe's Home Depot. You dont need a huge space to shape a surfboard, as shown in the photo above. The shorter the board, the easier it is to turn and the quicker it will recover from turning into planning.The wider, thicker, longer, and/or flatter the surfboard is, the better it tends to perform in slow and/or small waves; the narrower, thinner, shorter and/or curved the surfboard is, the better it tends to perform in fast and/or larger waves.Fins are also essential and highly determinant components in a surfboard, and, as such, should be considered as a part of the overall design. Measure the distance between the beam and the nose/tail with a T-square, using the shapers pencil to mark how much rocker you should mow.

Think of them as add-ons. It is still possible to make your workspace pleasant and functional. Thanks for posting this Wood Buddha.
vm gm5l*SNwNd&O! 3
|!M d00K Un 3q]is&t{&6q0:_Aog]s)tY(sqO+31,'&I`A 9P\Ne`oGhEV`Q\,L{1a5$i%?6VJ,S!sSx.axdL&z=b;*yf. So, weve created this Ultimate Guide on How To Make a Surfboardbut weve split it into five manageable chunks. Depending on the rail design of choice, you might want to further adjust the rail taper. Nowadays, most surfboards are built in factories, with the help of computers and power tools, under intricate shaping plans and meticulously calculated curing times, in temperature-controlled rooms a veritable production line. The shaping stand ends. Level the stringer by running a hand block plane over it. Brilliant. Check. Alternatively, use a 40-60-grit sanding paper, sliding it from nose to tail without stopping to scrub a single spot. Easy Peesy Japaneesy. Coming up next is the next is the final part of this series, the on how to build a surfboard: Sanding and Polishing. By doing all the aforementioned and cross-referencing it with your own research and ideas, it becomes a lot easier to make up your mind regarding the type of surfboard you want to build. Most people, depending on how they want the colouring, run a masking tape along the edge of the rail, but feel free to mask the entire bottom if you want. With your template ready, take some time to double-check all measurements and scrutinise the curve to ensure it has no dips. Everyone who is thinking about making a board, most definitely needs to either buy, or make a shaping stand. Use the latter to extend the bands into the nose and tail. I think so, but then again I've been spending a little too much time in the shed lately. This is where your idea will gain form; this is where you will put your craftsmans skills to use; this is where the progress of your project will be visible; this is where you will be covered in foam and dust and grinning like a five-year-old rascal. It's 1" particle board with paint on the bottom side to protect from wet grass. Instead, look up a professional glasser in your region; it will save you time and ensure your board is properly finished. The goal here is to flatten and even the laps as best as possible (many glassers use a wallpaper roller to help with this) so no air bubbles forming when you move on to laminating the deck. ), having a minimum amount of tools and materials or, rather the right tools and materials can make or break your project. You'll need two of these. This choice is important because it will determine the kind of technique you will have to use in the process freelap for clear glass jobs and cutlap for tinted ones. Laminating the bottom of the surfboardHeres where things get exciting, where the magic happens. For those who have opted for a coloured glass job (cutlap technique), try sanding as smoothly as possible since too much pressure on the laps can fade the pigment. Laying and cutting the fibreglassAlways begin the glass job at the bottom of your surfboard.
Sitemap 23